Grinding gears up to and including class 3
GBS Machining Services from Schiedam has developed a process for the production of gears and grinding gear sets. The technicians have worked closely together for this, so that they have succeeded in putting away a unique gear grinding process. We all know the methods such as end milling, and traditional gear grinding. Nowadays this also includes five-axis gear grinding for the lower classes. At GBS Machining Services we mill all kinds of parts, but grinding gears is also possible. New techniques are also making their appearance and machine suppliers are coming up with new gear grinding applications. Time for an update in the field of gear manufacturing. The GBS Machining Services process is particularly suitable for gears from module 1 to module 8. With the new process, we can help our customers deliver prototypes much faster. Normally you make gears with the help of gear grinding machines. Sometimes there is also an unusual gear, or close tolerances are required. So what you get is that we work with grinding machines. With grinding machines we can sharpen gears with great precision. This takes a lot of time at many companies, but at GBS Machining Services we make it our specialty to grind it as quickly as possible. If the customer has a specific job and is in a hurry, we cannot afford to take several weeks to grind a gear. That is why we specialize in speed and precision. The engineers at GBS Machining Services have now devised a new process: grinding gears from the material supplied by our customer or by ourselves. Sometimes we receive a ready-made drawing, but sometimes we also ensure that we re-engineer it. What the drawing should in any case have is a specific tooth shape and module. With this drawing we determine the type of grinding stone for the gear wheel, and which grinding bench is free at what time. Because sometimes it happens that there are several urgent jobs in between, and then it sometimes becomes fitting and measuring. This often does not lead to problems, because we have several grinding machines spread over several locations. So if one location does not have space to grind the gears, the other location often still has space for it. In addition, if necessary, our staff works night shifts to have the gears sharpened on time. In the meantime, we ensure that after grinding, we measure the module and the dimensions of the gear wheel directly on the grinding machine, so that we quickly know whether the gear grinding has been successful. After grinding the gear wheel, the grinding machine replaces the grinding stone for a measuring needle. This measures all ground gears. The grinding stone is corrected if necessary. The next step is to harden, and sometimes even double-harden, the gear, this is to ensure that after grinding the gear, the outside is provided with a robust hard outer layer, while the inside remains soft and tough. In that case, the gear does not break off quickly. After hardening, the gear is reground. Regrinding the gear wheel ensures at a microscopic level that the gear wheel conforms to the correct size. This is ultimately important for the life of the gear. In addition, almost all types of head and foot corrections can be met, but that's another topic. GBS Machining Services regularly grinds gear wheels from solid material. Despite the labor-intensive process, we are quick at this. Being able to sharpen gears quickly is important because longer waiting times often mean longer downtime for customers. This in turn means that they lose a lot of money on this. Sometimes a million euros a day. We often use this method of grinding gears for single pieces. Our grinding bench operators therefore adjust the gear grinding benches several times a day, on the next workpiece. This automatically means that the software of the machine must be adjusted. Special sharpening software, a Niles ZP40, was installed on the machine for sharpening. With that we want to say that we at GBS Machining Services do not always keep up with the trends in gear manufacturing. For example, automation is an important topic nowadays, and when grinding large series of gears it is logical that this goes well. However, in the area of single pieces, on which GBS Machining Services focuses, this is less important. For example, we could invest in machines with a pallet system and so on, but often when the grinding machine is running, the grinder has time to deburr or prepare the previous or next gear. The Niles ZP40 as we see it at GBS Machining Services is therefore automated in the sense that it is CNC controlled. A bit further on we see a Nilpes ZP70 grinding large-format gears. Think of about 4 meters in diameter. The production times for grinding these gears are short, because we are set up for this. When the machine has finished grinding the gears, from the previous product, the finished product turns. After that, the gear is immediately prepared for shipment. Gears are expensive products and therefore we find it normal to ensure that the gear arrives neatly at the customer, neatly deburred and a layer of oil over it, and packed symmetrically. We also apply a completely new way to grind internal gears at GBS machining services. This is very special, because grinding the internal teeth of gears has been a difficult task for a long time. There is already an article about grinding gears in itself and we do that here too. However, we limit ourselves here to the principle of grinding gears. It is as follows: the tool is a grinding stone installed on a grinding bench. In contrast to stabbing, the grinding movement is not generated. The grinding stone on the machine as the tool generates a high speed, which grinds the gears and thus enables the end product. During the grinding movement of the gear grinding tool, the gear remains stationary until the toothing has been ground deep enough. A requirement here is that the sharpening stone has the correct shape and roughness. A rough sharpening stone ensures that it is easy to sharpen deeply and this saves time. However, a fine sharpening stone can be used to sharpen gears more precisely. Each stone therefore has its degrees of angles that are suitable for certain gears. With this grinding wheel, a clearance angle is achieved between the tooth flanks of the tool and the tooth flanks of the workpiece. This is called the gear grinding angle. In addition, the rapid movement of the gear ensures time savings. On the one hand, the distance between the axes of the workpiece and the tool must be set. On the other hand, the sharpening stone must be placed very precisely. This process of moving the tool along the axis of the workpiece requires twisting of the tool or workpiece. Although the gear grinding method may seem simple at first glance, it is quite a complicated process. With normal gears, grinding is a process in which this complexity must be embraced, as it otherwise leads to poor chip properties.
Machine factory for grinding gears
Gear grinding For grinding teeth, we use several Niles ZP machines, as mentioned earlier. We have a small machine at our location in Oud-Beijerland, where we have two large grinding machines at the location in Schiedam. These modern grinding machines can grind gear wheels from module 1 to 50. And the gear wheels are ground up to class 3.
At GBS Machining Services we have multiple technicians working, even in shifts. They specialize in grinding large gears. You could safely call them true artists, when you see with what finesse they deliver quality products. It can grind external teeth of gears with a maximum diameter of 2000 mm.
The Niles grinding machine has a grinding stone for gears with a considerable mass. Also the grinding spindle and motor. The Niles grinding machine can sharpen gears from module 1 to 50 and when you put an experienced machine driver behind it, quality is guaranteed
Grinding gears by true technicians
The machine uses the latest software with which, in addition to grinding gears, it can also measure teeth and therefore immediately check whether the gear has been properly produced. In addition to costs, this also saves a lot of time. With a maximum grinding wheel size of more than 350mm, we can grind the largest gears.
Gears grinding
Machinefabriek GBS Machining Services is a producer of metal workpieces that need to be machined quickly and professionally in general, but we also have a separate division for grinding gears. This is also necessary, given the specialism that well-ground gears require. GBS Machining Services continuously invests in innovation, in order to better serve customers in this way. These investments are therefore made in a better quality offer by means of training and purchasing machines. But also grinding the width of the range in gears.
The machine factory has not always focused on grinding gears. It started as a consortium of different engine overhaul companies. Later GBS Machining only started grinding with gears. The CNC machines from Niles provide ultimate stability and no play.
The modernization of the machine factory a few years ago already ensured that grinding gears and in principle became a breeze. This also makes it possible to make products that require more knowledge such as high speed gearbox gears and take on rush jobs.
CNC grinding of gears
To be able to place the CNC grinding machines and to have the department run as smoothly as possible, the gear grinding machines were placed as close to each other as possible. In addition, a large part of the floor was reserved for storage and deburring of the gears. The gear grinding machines have been around for a number of years now, but are still among the best in their class. Machinefabriek GBS Machining Services is therefore prepared to grind your gears, to check products, and to reverse engineer gears where the drawing is missing.
Why grinding gears at GBS Machining Services?
The measurement results showed that the gear grinder works best. This CNC profile grinding machine, a Niles ZP40, grinds beautiful gears up to a diameter of 40000mm. The full profile grinding machine can grind from module 1 to 50. The grinding bench can also grind the teeth from solid material. Our ground gears can undergo quality control on both the measuring machine and the grinding machine.
The purchase of the grinding machine was a considerable investment at the time, but paid off quickly.
The quality and efficiency of grinding gears have become a lot better with these grinding machines. CNC controlled means that you can count on shorter times and more precision. Because we make fewer mistakes as a result, we can also lower our prices. The grinding machine increases the possibilities of grinding gears by allowing disc cutters with inserts to be mounted on it.
GBS Machinig Services quickly delivers single pieces or small series of gears according to drawing or model. All conceivable teeth can be ground. So you can also leave the hardening to GBS Machining Services. We can even arrange the inspection of the gears for you. We pronounce the dimensions in module. This is important because it is also possible to machine non-standard sizes. We are a machine factory that, in addition to boring, turning and milling, also specializes in gears. Our customers mostly come from industrial sectors. Take a look at the stories in the customer case section, in which several success cases are highlighted.

Gear grinding
Grinding gears of all sizes
Why work with GBS on gear grinding?
GBS has experience in making all kinds of corrections, such as of head and top corrections, longitudinal corrections and chamfers.
As a result of our specialization in gear grinding, we can reach greater accuracy than with milling teeth. GBS can grind gears with accuracy up to Class 3.
GBS has a MAAG measurement setup to apply blueprints on the gears.
GBS can machine gear teeth in a range from 0 to 4000 mm.
GBS has more than 20 experience with complex types of gears, such as: spline gears, crown gears, V-gears, planetary gear systems, curvic plate couplings, panama wheels and internal gears.
Grinding gears with GBS means more than just execution; we can advise you on the type of correction for your gears and thus maintaining your installation in optimal condition.
GBS understands that gears with complex types of teeth are often single pieces and speed is crucial in their repair. It is also common that drawings are unavailable. GBS has its own engineering department to calculate complete drives and gearboxes. In addition, if desired, we work in 24-hour shifts to carry out the work for you as quickly as possible.

About gear grinding
There are many different types of teeth; all with their own benefits and functions. Due to the complexity of gear grinding, we have a dedicated team of specialists committed to gear grinding.
The business unit for gear grinding is supported by the engineering department. In addition to straight, bevel, internal and external gear grinding, the engineering department specializes in curved gear grinding. Therefore we can also offer bevel gear grinding.
To translate engineering into a concrete program, we employ a mathematician with 20 years of experience in gears. This is how the most accurate programs are written to bring your gears back to optimal condition.
Gear grinding as a method for repair
Gear damage often has far-reaching consequences for your installation. For example, it can happen that an installation can only run at a certain percentage of its capacity. A lot of collateral damage can also occur when the gears are running in. Making positive or negative corrections to gears on time is crucial to increase the life of your installation as a whole.
Pinions
In case there is damage to the teeth of the gear, it is important that a well-considered choice is made as to the type of correction to be performed. Pinions with less than 20 teeth are often very accurate. Yet, when undercut occurs, this results in breakage sensitivity and a shorter life of your pinion gear. Pinions with more than 20 teeth are not subject to undercut. Due to larger diameters, deviations as a result of clearance in the drive, for example, will be magnified.
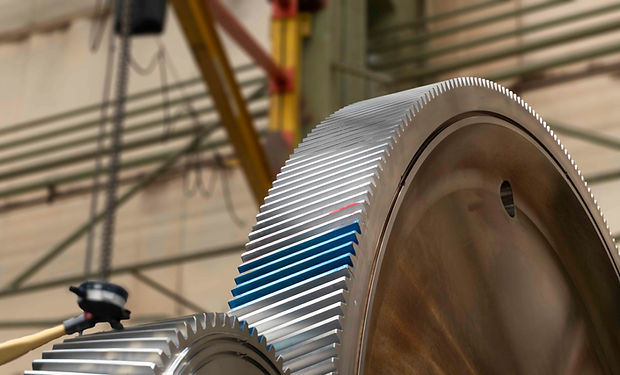
Customer case
Toothing is a challenging profession in which one never stops learning. View a customer case in which Wolter takes you on a complex gear project; highlighting the strength of GBS's advisory role.